Auto’s veranderen, en hun banden rollen mee. Als ons vervoer straks elektrisch en autonoom wordt, nemen ook de eisen voor banden toe. Fabrikanten timmeren aan de weg.
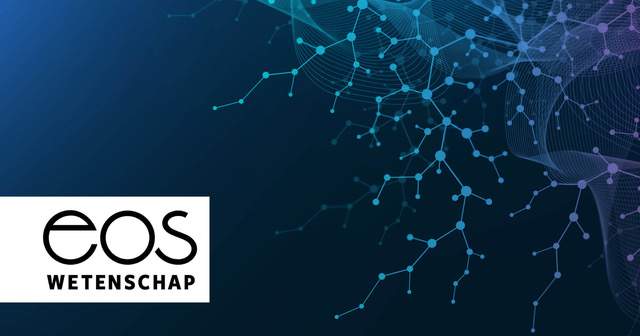
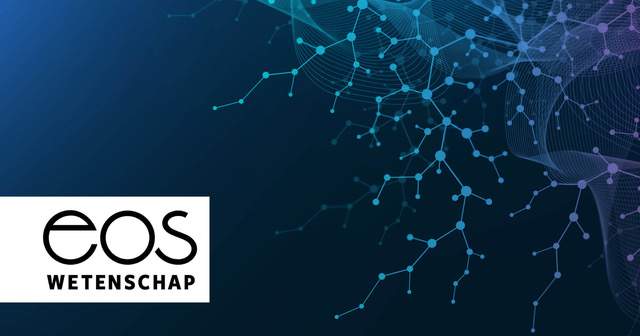
Grofweg 20 procent van de brandstof in de tank gaat verloren door de rolweerstand van banden
Het industriegebied Ladoux kijkt uit op een paar van de tachtig vulkanen van de Chaîne des Puys. Ze vormen het spectaculaire visitekaartje van de Franse Auvergne. Een paar kilometer van hier, in Clermont-Ferrand, ontwikkelden twee broers in 1895 de eerste rubberen autoband ter wereld. Vandaag, 123 jaar later, rollen uit de fabrieken van André en Édouard Michelin jaarlijks 170 miljoen banden. Daarmee is Michelin de tweede grootste bandenproducent ter wereld, na het Japanse Bridgestone. Tel daar nog die andere gigant, Goodyear, bij, en je hebt 40 procent van de hele bandenproductie op een lijstje.
De banden zijn niet alleen bestemd voor auto’s. Ook trucks, bussen, Formule-1-racewagens, spaceshuttles, landbouw- en legervoertuigen en fietsen rijden of vliegen rond met Michelin-materiaal. De banden vind je overal – Michelin heeft dan ook inmiddels afdelingen in zeventien verschillende landen. Maar het hoofdkantoor heeft de Auvergne nooit verlaten. Hier in Ladoux bevindt zich het wetenschappelijke hart van het concern. Het zogeheten Centre de Technologie Michelin strekt zich uit over een afstand van ruim driehonderd meter.
Aan weerszijden van de hal, die toepasselijk Innovation Street heet, hebben 1.700 knappe koppen – technologen, scheikundigen en informatici – hun werkplek. Elk van de tachtig afdelingen richt zich op een specifiek onderdeel, zoals ‘winter’, ‘polymeren’, ‘truck’ en ‘sport’.
Cyrille Roget, die de communicatie van de onderzoekscentra voor zijn rekening neemt, leidt ons rond. Een dorp, zo noemt Roget deze plek, doelend op de winkeltjes, het grote restaurant en de kapperszaak aan het begin van de Innovatiestraat. Klinkt charmant, maar bezoekers raken hier niet zomaar binnen. Zij dienen hun paspoort bij de ingang in te leveren, gaan verplicht op de foto en, eenmaal binnen, zetten ze geen stap zonder dat iemand hen in de gaten houdt.
Die strengheid heeft een reden. ’72 procent van alle innovaties van Michelin komt uit dit gebouw’, zegt Roget. Naast Bridgestone en Goodyear zijn er nog tientallen andere, kleinere kapers op de kust. Kortom: genoeg nieuwsgierige aagjes die er veel voor zouden hebben om de hier ontwikkelde technologieën te bemachtigen. Het is een risico dat een bedrijf met 130.000 personeelsleden en een jaaromzet van 21 miljard euro zich gewoon niet kan permitteren.
Rolt lekker
De ‘innovaties’ waaraan Michelin werkt, zijn gericht op een aantal streefdoelen. Banden moeten onder meer veiliger en comfortabeler worden, maar ook zuiniger en milieuvriendelijker. Een belangrijk begrip voor die laatste twee mikpunten is rolweerstand. Op de weg zorgen banden voor frictie. Het rubber wordt warm, en dat leidt tot energieverlies.
Vandaag gaat grofweg 20 procent van de brandstof in een tank verloren door de rolweerstand van banden. Michelin en andere producenten willen dat percentage reduceren. Naar 0 procent kunnen ze echter nooit – banden moeten het wegdek nu eenmaal raken, en dan nog heb je af te rekenen met aerodynamische weerstand, inwendige wrijving en de zwaartekracht. Er is ook nog de traagheidskracht: de extra grip die banden nodig hebben in bochten. Toch kan een subtiele verandering aan bijvoorbeeld het profiel van een band al heel wat zoden aan de dijk brengen. En er zijn nog ingrepen mogelijk: de bandmassa verkleinen, de flanken versmallen, een ingrediënt toevoegen waardoor de band ‘lekkerder rolt’. ‘Begin jaren 1990 beleefde de bandenindustrie op dat vlak een doorbraak’, zegt Roget. ‘Door nanodeeltjes kiezelaarde aan het rubber van de banden toe te voegen, konden we aanzienlijk op brandstof besparen. Een bijkomend effect was dat de remefficiëntie op natte wegdekken vergrootte.’
Aan zulke evoluties gaan lange processen van trial and error vooraf. ‘Voor die kiezelaarde hebben we erg lang gezocht naar de ideale verhoudingen. Je kon het vergelijken met het maken van een cake, waarbij het kneden en mengen van de ingrediënten de kwaliteit van je cake bepaalt. Wanneer voeg je wat toe en onder welke omstandigheden? Met zulke vragen zaten we toen we kiezelaarde met rubber begonnen te mengen.’
SUPERSLIM, PEPERDUUR
De auto-industrie verandert voortdurend, en de bandenfabrikanten moeten mee evolueren. De vondst van de kiezelaarde kwam niets te vroeg: de laatste jaren zijn auto’s harder gaan rijden en zijn ze zwaarder dan ooit. Vandaag bereidt Michelin zich voor op de doorbraak van elektrische wagens. Daarbij komen heel wat nieuwe uitdagingen boven water. Ingenieurs kunnen bijvoorbeeld niet zomaar de nieuwste duurzame banden onder een e-car pleuren. Elektrische auto’s rijden bijvoorbeeld heel wat stiller, waardoor het monotone lawaai van ‘gewone’ banden des te luider zou weerklinken. Verder vereist de aandrijfkoppeling van een elektrische auto voldoende stevig rubber. Een auto is een kostbare investering; je wil er niet elke tweeà drieduizend kilometer mee naar de garage voor nieuwe onderdelen.
Nog zoiets waarmee banden moeten bijbenen: de toenemende mate van autonomie in auto’s. In moderne voertuigen wemelt het van de knoppen, sensoren en andere computergestuurde elektronica, die inzittenden comfortabel en veilig van A naar B moeten brengen. De functies zijn zo nauw met elkaar verbonden dat de auto in staat is taken van de bestuurder over te nemen. Auto’s zullen zelfstandig van baan kunnen wisselen – of juist niet als er een voertuig in de blinde hoek zit –, ze reageren op verkeersborden en parkeren volautomatisch in de krapste plekken.
De stap naar volledig zelfrijdende auto’s is niet langer een utopie, zeggen deskundigen. Maar voor dat moment aanbreekt moet op z’n minst één auto-onderdeel worden verbonden met het boordcomputersysteem: de band. Zogenaamde ‘interconnected tires’, banden met ingebouwde zendersystemen, zitten al op grote mijn- en landbouwmachines. Ze zijn peperduur – meer dan 25.000 euro – en, door de immense ladingen die ze moeten torsen, kwetsbaar. Bij elke bar onder de noodzakelijke druk neemt de levensduur van de band met 20 procent af. Continue monitoring is dus cruciaal. Met geavanceerde zenders in de banden kan dat heel eenvoudig, vanuit een centrale controlekamer.
Die technologie kan zijn weg vinden naar personenauto’s. Bestuurders krijgen gegevens als druk, temperatuur, profiel en de toestand van het wegdek, direct op hun dashboard te zien. Al die informatie komt dan van de band zelf.
Wanneer ten slotte over een tijdje zelfrijdende auto’s de weg op mogen, dan zullen die adequaat moeten kunnen reageren op plotselinge gladheid of kuilen. Zover is het nog niet, denkt Roget. ‘Je kunt bijvoorbeeld niet hebben dat je door de auto wordt geslingerd omdat die op het laatste moment heeft beslist uit te wijken voor een obstakel.’ De banden moeten zulke plotse manoeuvres in alle weersomstandigheden kunnen opvangen.
Heilige graal
Zelfs als al die problemen van de baan zijn, is er nog de eeuwige kwestie van de lekke band. Het is de irritantste kwaal van elke autoband, en als automobilist heb je dat maar te slikken. Bandenonderzoekers nemen daar geen genoegen mee. Sinds jaar en dag zoeken Michelin en andere producenten naar een antwoord op deze tekortkoming.
Een aantal provisorische tussenoplossingen passeerde al de revue. De run-flat tire heeft een stijve, versterkte rand, waarop een auto met een lekke band toch nog een paar honderd kilometer kan doorrijden. Praktisch, maar ook oncomfortabel, omdat vering ontbreekt. En blijf je te lang doorrijden, dan is de band niet meer te repareren. De self-sealing-autoband was nog zo’n vondst. Als je over een spijker of een ander puntig voorwerp rijdt, zorgt een speciaal afdichtmiddel op waterglycolbasis ervoor dat de band zich onmiddellijk over het gaatje sluit. Heel inventief, al zijn er nog steeds tekortkomingen. Gaten groter dan vijf millimeter kan het middel niet aan, en je moet alsnog naar de garage om de band te laten maken.
Ruim tien jaar geleden leek het dan toch zover te zijn. Had Michelin dan eindelijk de heilige graal gevonden die de lekke band definitief tot het verleden zou verbannen? In 2005 introduceerde de bandenfabrikant de Tweel, ofwel de luchtloze band. Het geheim zat ‘m in de stijve maar elastische spaken die de luchtband vervingen. Toen de eerste golf van opwinding voorbij was, hoorden we evenwel bitter weinig over de Tweel.
De banden bleken nog lang niet geschikt voor personenauto’s. Zodra je een snelheid van 50 kilometer per uur haalt, gaat de auto te veel vibreren. Bovendien veroorzaken de banden een enorm lawaai en raken ze oververhit. En hoewel er al wel grasmaaiers, shovels en andere langzaam rijdende voertuigen op luchtloze banden rijden, duurt het volgens Roget nog zeker vijftien tot twintig jaar voor we bij de garage Tweels onder onze auto kunnen laten zetten.
Vandaag werkt Michelin aan een ander concept. Roget leidt ons naar een vitrine, met daarop een in hemelsblauw uitgevoerde band. De ‘Vision’, zoals de conceptband heet, is duurzaam. Onder het exemplaar op de vitrine staan potjes met ingrediënten: natuurrubber, bandenafval, bamboe, elektronisch afval, blikjes, melasse, plastic afval, hooi, cardboard, hout, papier en textiel.
Nog opvallender: de Vision is volledig 3D-geprint. Dat heeft belangrijke implicaties. Het zou betekenen dat als de band versleten raakt, je gewoon een nieuwe profiellaag kunt laten printen. En als de buitentemperatuur naar beneden duikt, laat je op dezelfde manier een winterbandprofiel printen. De band zelf hoef je niet meer te verwisselen. ‘Met de Vision gaan we terug naar het begintijdperk, waarin de band ook uit één geheel bestond’, zegt Roget. Volgens hem heeft Michelin grote plannen met de Vision, maar moet er eveneens veel aan worden gesleuteld.
Zevenduizend sprinklers
We begeven ons naar het midden van de enorme hal van het onderzoekscentrum. Door een glazen vloer kijken we naar een weg die zich onder onze voeten uitstrekt. Een motor schiet op volle snelheid langs. Het had ook een truck kunnen zijn, zegt Roget, of, zoals we even later zelf ervaren, een personenauto. Dagelijks rijden professionele testrijders rondjes op de 21 circuits in Ladoux. De totale lengte is 43 kilometer.
Michelin beschikt over een wagenpark van driehonderd voertuigen. Soms huurt de fabriek de plaatselijke ijsbaan om banden uit te proberen. Ook in Finland en Spanje stelt Michelin zijn testproducten bloot aan extremere weersomstandigheden.
Wij gaan vandaag in een BMW 193 voor het natte circuit, dat met behulp van zevenduizend sprinklers over ruim vier kilometer constant onder water staat. Bestuurder Florent Dugat geeft gas. Terwijl hij op volle snelheid en met opspattend water rondom ons slipt en glijdt, praat hij rustig verder. ‘Een gemiddelde werkdag bestaat uit vier testritten van twintig minuten. Het gaat ons vooral om de ervaring: hoe houden de banden zich bij hoge snelheden, in scherpe bochten en, zoals nu, bij aquaplaning? Tussen de tests door verwisselen we de banden en schrijven we de rapporten.’ Terwijl wij na afloop licht duizelig op adem komen, is Dugat er alweer vandoor in zijn auto. Nog een paar rondjes, en dan weet hij of de banden door mogen naar de volgende ronde.
De autoband in vogelvlucht
1839 Zonder vulkanisatie geen autoband. Na bijna twee eeuwen is het verhitten van natuurrubber met zwavel dé methode om soepel, stevig en dus bewerkelijk rubber te verkrijgen.
De methode staat op naam van de Amerikaan Charles Goodyear (1800-1860).
1895 De eerste rubberen autoband. De Michelin-broers waren meesters in marketing. Ze rustten als eersten ter wereld een auto uit met rubberen banden en namen deel aan de Parijs-Bordeaux-Parijs-straatrace. Winnen deden ze niet, maar kort daarna was hun pas opgezette concern wel de grootste bandenfabrikant van Europa. Een halve eeuw lang zou de autoband bestaan uit een binnenband met lucht en een beschermende buitenband met een diagonaal profiel.
1949 Van diagonaal naar radiaal. De eerste decennia reden auto’s op banden waarvan de draden schuin (diagonaal) ten opzichte van de rijrichting van de auto stonden. Dat leverde veel weerstand op, waardoor de stugge band te warm werd en voortijdig sleet. Na de Tweede Wereldoorlog introduceerde Michelin de radiaalband, waarbij stalen koordlagen loodrecht op de hiel (het binnenste deel van de band) en dus haaks op de rijrichting werden gezet. De band had een veel betere grip op de weg. Tegelijkertijd daalde de wrijving en dus het energieverbruik. Wel had de radiaalband een extra staalgordel nodig, omdat de gevoeligheid voor oneffenheden op de weg groter bleek. Radiaalbanden werden al snel de nieuwe standaard.
Tweehonderd ingrediënten
Een autoband bestaat allang niet meer uitsluitend uit natuur- en synthetisch rubber. Er gaan tegenwoordig meer dan tweehonderd ingrediënten in, van chemische tot natuurlijke grondstoffen. Zo is het koolstofpoeder carbon black een belangrijk vulmiddel. Het is verantwoordelijk voor de zwarte kleur van de band. Belangrijker is dat het slijtage vertraagt en afbraak van het rubber door ultraviolette straling tegenhoudt. De precieze bereidingswijze, de manier waarop en de staat waarin de grondstoffen worden gemengd, verwarmd en gevulkaniseerd, vormt het kernkapitaal van alle bandenfabrikanten en is dus topgeheim.